A deep dive into the continuous improvement process (CIP)
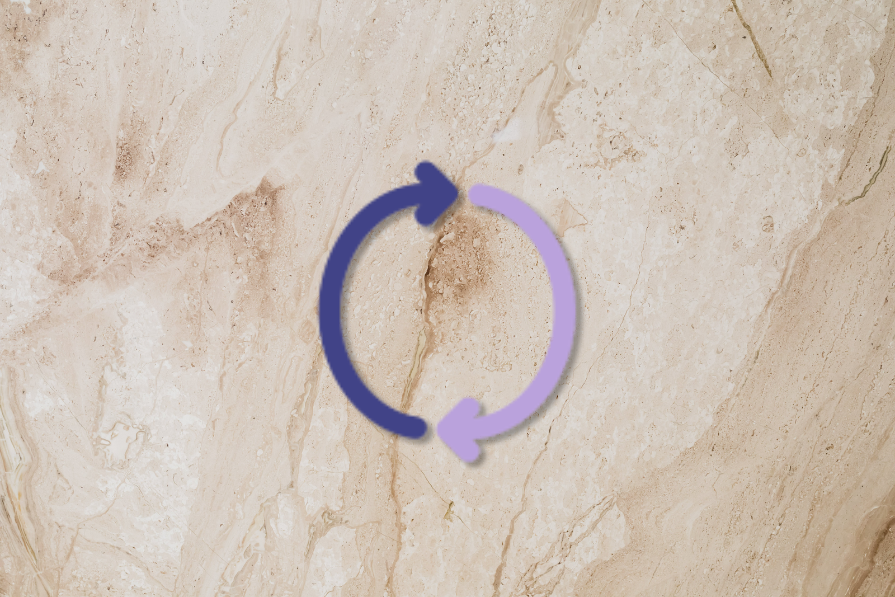
Deep Dive into Continuous Improvement Process (CIP)
What is the Continuous Improvement Process (CIP)?
The Continuous Improvement Process (CIP) is a methodical approach to identifying and addressing opportunities for improvement within an organization. It involves constantly reviewing and enhancing processes, products, or services to increase efficiency, quality, and customer satisfaction.
5 Steps of the Continuous Improvement Process
- Gather Data: Without data, it's challenging to pinpoint areas for improvement.
- Define the Problem: Focus on one or two key areas for improvement.
- Set Goals: Establish clear success criteria and baseline for improvement.
- Analyze and Refine: Continuously evaluate performance and adjust the improvement process.
- Implement Changes: Ship features or implement processes based on analysis and refinement.
Principles of the CIP
- Customer Focus: Understand and address customer needs.
- Employee Engagement: Involve employees at all levels in fostering a culture of improvement.
Tools and Methodologies for Continuous Improvement
- Kaizen: Focuses on incremental, easy-to-implement changes.
- Six Sigma: Aims to remove defects and improve quality using statistical methods.
- Lean: Identifies value, builds efficient workflows, and promotes continuous improvement.
Challenges in the CIP
Implementing a CIP may face challenges, such as resistance to change. Leaders must communicate the importance of improvement and gain buy-in from all team members.
Key Takeaways
Successful implementation of CIP is vital for organizational relevance and competitiveness. Involving employees in problem identification and solution development, utilizing data and analytics, and fostering a culture of continuous improvement are key aspects for success.